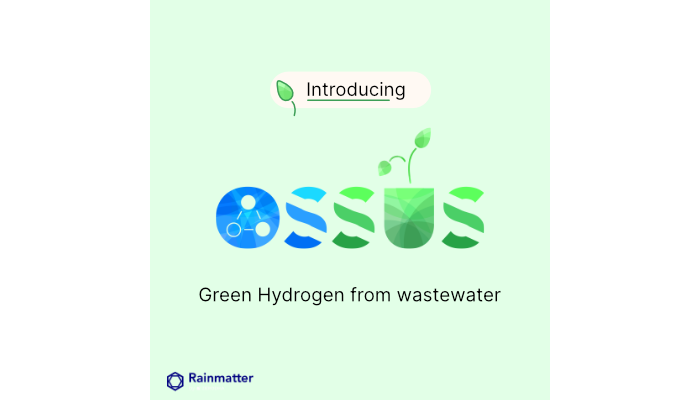
Introducing Ossus
Since last year, for every investment we have made, we put up a note explaining why we invested, and what the startup does. We have often added context to the investment we made since we feel it is important not only to be investors but also to understand the larger picture of what the startup is trying to achieve. In almost all cases, we have tried to support long-term research, R&D, and product development out of India. And if we have to describe our investment in Ossus in one word, it would be – Moonshot.
By now, it is clear that a large chunk of time across the world is being spent thinking about energy requirements, and optionality around energy sources. That means, not only do we need increasing amounts of energy, but we need to diversify the sources to find better and cleaner resources. Easier said than done.
However, there are still pockets of research in India aiming to find a solution to these problems. Ossus is not just a Green Hydrogen startup, but a research team that is looking to solve for energy requirements of the future, backed by half a decade’s worth of meticulous research. They not only managed to put together a reactor that ingested wastewater and spit out hydrogen but managed to do it at a fraction of the cost and energy required in most other cases. Well, they also managed to find a few clients early on – that is the cherry on the cake.
We invested in Ossus in 2021, and continue to back them with a recent investment that we did, to double down on our conviction in the team. Here is a slightly long description of the work Ossus does, from Suruchi, founder of Ossus.
At Ossus, we have a singular goal to make green hydrogen available to industries as a ready replacement for fossil fuels like natural gas and coal. Our product, the OB HydraCel, eliminates dependency on imported, expensive equipment and pure water for green hydrogen production by utilizing the organic content of industrial effluents (wastewater generated during industrial operations) as a feedstock or source.
When we started, we had a singular conviction – to a new industry standard in the production and consumption of hydrogen gas as a replacement for fossil fuels and the last 7 years have made that conviction stronger with the help of our partner clients spread across many sectors in India including Steel, Chemicals, Upstream Oil and Gas amongst others.
At the risk of sounding obsessed though, we love the hydrogen molecule, so to talk about Ossus first requires a little dip into what makes hydrogen so special.
Hydrogen is a gas, just like natural gas that is packaged in cylinders that we use in our homes for cooking. It is a gas when burnt produces no carbon dioxide, only water vapor. Hydrogen is special – because it is the most energy-dense molecule on planet Earth. Hydrogen has nearly 3 times more energy when compared to diesel and petrol. If we were to replace natural gas as cooking fuel in our homes we would need as little as 5 kilograms of hydrogen compared to the 25 kilogram cylinders of natural gas that we have come to become familiar with. In terms of emissions, while diesel cars emit around 120 grams of CO2 per kilometer and petrol cars emit around 200 grams per kilometer, if hydrogen were used in vehicles it would produce zero emissions. With such benefits then, it would appear that we already have the perfect replacement for fossil fuels and the challenge of climate change can be met head on. Right?
Well, this is where the differentiation of hydrogen from conventional fossil fuels begins. There are two problems with hydrogen – what is used to make hydrogen and how hydrogen is handled.
Cooking with a single ingredient
Hydrogen in the decarbonization context is often dubbed green hydrogen and if you were to look up the definition of green hydrogen it would refer to an electrolyzer – a device used to split water (H2O) into its native components hydrogen and oxygen. The amount of electrical energy required to split water into a kilogram of hydrogen (55 kWhr) is nearly double the daily power consumption of an average 3-bedroom household in a metro city in India (20-30 kWHr).
India’s National Green Hydrogen Mission has set a target of 5 Million Tonnes of Green Hydrogen, revised to 7.5 MMTPA in 2024 to be produced indigenously by 2030. The projection of price – benchmarked as the Levelized Cost of Hydrogen or LCOH is also based only on the use of electrolyzers to produce hydrogen.
However, producing 7.5 million tonnes each year would require an additional installed capacity of 1130 GW and 75 billion liters of ultrapure water each year. India currently only has a total installed capacity of 106 GW (until February 2022), compounded by the fact that 550 million people go without access to clean drinking water, let alone for energy production. There is also a larger sustainability issue here if electrolyzers were used as the only technology for the production of green hydrogen.
To understand why, let’s imagine you’re running a restaurant and you decide to only cook with one ingredient, say potatoes. Potatoes are versatile, they can be mashed, baked, fried, or roasted. But as you focus more on potatoes, you start encountering a few problems. You encounter the problem of resource limitations and are dependent on a single ingredient. Potatoes require a lot of space to grow, a specific climate, and a steady supply of water and fertilizer. If the weather is bad, or if potato prices rise, you’re in trouble because your entire restaurant depends on that one ingredient.
In the case of water splitting, you’re dependent on electricity and water to produce hydrogen. If the electricity supply is unreliable or expensive, or if freshwater becomes scarce, it can drive up the cost or even halt hydrogen production. Similarly, electrolyzers are expensive to build and operate. They require a lot of energy to produce hydrogen, and if the price of renewable electricity rises, the cost of hydrogen will increase as well. Just like fluctuating potato prices can impact the price of your meals, electricity prices affect the cost of producing hydrogen through electrolysis.
Now imagine, if everyone suddenly wanted potatoes, you’d run out of space to grow them, or your supply chain could break down. You can’t scale up your menu just by growing more potatoes; you’d need new farming techniques, equipment, or even a different approach to meet demand.
Water electrolysis faces similar scalability challenges. Right now, electrolysis is energy-intensive, and scaling it up to produce large amounts of hydrogen at a global level is not straightforward. The capacity for renewable electricity may not be able to keep up with the demand, and it takes time to scale the technology. Just as potatoes can only feed so many people efficiently, water splitting is currently limited in how much hydrogen it can produce at scale. Hydrogen production via water splitting is also vulnerable to external factors. If there’s an energy crisis (e.g., electricity prices soar or supply becomes inconsistent), or if there’s a shortage of water resources, hydrogen production can become more expensive or even impossible.
At Ossus, we instead focus on the use of organic waste (industrial effluents), as the feedstock for hydrogen gas production and use as little as 2 kWHr for producing a kilogram of hydrogen. We’re not just adding another ingredient to your menu; we’re also turning waste into a resource. Instead of growing new potatoes, you’ll find value in things that were previously discarded.
When we started Ossus back in 2017, the opportunity we zeroed in on was the widespread availability of industrial wastewater, which was going unused.
Circularity then was a theoretical concept, instead, wastewater was considered a necessary evil, with associated high, unavoidable costs and the threat of stringent legal implications of leaving wastewater untreated. From our perspective, this was a resource (India generates about 13,500 million liters per day (MLD) of industrial wastewater from manufacturing clusters alone) – ideal as a raw material for hydrogen production using our technology for being closely controlled. Our conviction was supported by our first customer – Tata Steel and our journey with them has led us this far – to a total installed capacity (as of November 2024) amounting to nearly 2000 kilograms per day, across 3 states in India.
Need for Containerization
Coming back to the second problem, despite the advantage of high energy density, hydrogen is plagued with being low in volumetric density. To understand just how low, let’s say you were standing in a 200 sq. ft room, with a 10 ft high ceiling and decided to fill the room (for kicks and curiosity) with natural gas, petrol, diesel, and hydrogen sequentially (disclaimer: at the risk of stating the obvious, please do not attempt this!). When measured, this room would hold 40 kilograms of natural gas, 41440 kilograms or a whopping 41 tons of petrol 46000 kilograms or 46 tons of diesel, and a measly 5 kilograms of hydrogen.
Now, why should this matter? It does not in any way take away from the efficacy of hydrogen as a replacement for each of these fossil fuels. What it does, is to take away the ease with which hydrogen can be produced, stored, and transported. Let’s use an analogy to understand why this is a problem.
Think of fossil fuels as large shipping containers filled with energy. These containers are standardized and efficient, so you can pack a lot of goods (energy) into a small, easily transportable container (e.g., a petrol or diesel tank in a car).
Hydrogen, on the other hand, is like a cargo of loose items that are scattered and unorganized. It takes up much more space to store the same amount of energy as a packed container of fuel. In this analogy, the loose items are like hydrogen molecules, which have to be packed into large, bulky containers (high-pressure tanks or cryogenic tanks) to make hydrogen energy-dense enough for practical use.
The problem here is that to solve this, you need to compress or liquefy the hydrogen (like trying to organize and fit those loose items into the right size container), but that takes energy and is not as efficient as simply filling a container with something that already fits the standard shape and size (like fossil fuels). This affects hydrogen’s ability to compete with fossil fuels.
Fossil fuel infrastructure is already well-established and efficient. In contrast, hydrogen’s low volumetric energy density means that it requires new infrastructure (e.g., high-pressure tanks or cryogenic storage systems) that are costly and energy-intensive to maintain, which raises the overall cost of hydrogen delivery.
With hydrogen, much of the energy is lost in the process of compressing, liquefying, and storing the gas. It’s like using energy to organize loose items before they can be shipped, whereas a standardized shipping container doesn’t need much additional handling.
At Ossus, just like containerization, we have packaged the production of hydrogen to a small footprint (10 square feet for 50-1000 kilograms of hydrogen), which allows for a retrofit of our plant (a self-contained production unit for green hydrogen) less than a kilometer away from the point of consumption. The challenges associated with the need for hydrogen compression, storage, and transportation are eliminated and replaced by transporting wastewater to our plant, allowing for efficient, standardized utilization.
Our early work began with the goal of producing green hydrogen for the steel sector (along with recycling the effluent). The steel industry accounts for 7-9% of global CO₂ emissions, primarily from coke use in blast furnaces. The steel sector is traditionally reliant on coal (particularly coke) for the reduction of iron ore in blast furnaces, which releases large quantities of CO₂. In India, around 70-75% of steel production happens via this method, contributing significantly to carbon emissions.
Green hydrogen injection into blast furnaces offers a significant opportunity for reducing carbon emissions in steel production, particularly for traditional blast furnace processes, which are among the highest industrial sources of CO₂ emissions globally. This process of hydrogen injection can contribute to a substantial reduction in carbon dioxide (CO₂) emissions by partially replacing coke (which is made from coal) with hydrogen as a reducing agent in the iron ore reduction process.
If 30-50% of the coke is replaced with hydrogen, emissions could drop by approximately 30-50% from the reduction process alone. This could translate to overall emissions reductions of 20-30% for the steelmaking process, depending on the specific technology and operational conditions. As of 2023, the cost of green hydrogen is about US$3-6/kg of which road transportation (including compression) contributed between US$3.50 and US$5.00 per kilogram.
At Jamshedpur, the HydraCel plant was installed (and continues to be scaled up) less than 0.5 kilometer away from the blast furnace. By eliminating compression and producing directly for blast furnace injection, we were able to offer green hydrogen at US$1.4 per kilogram in this project. When scaled up to full capacity the OB HydraCel Bioreactors will produce a minimum of 5040 TPY of Green Hydrogen which will be injected into the blast furnace and help in replacing 19800 TPY of coke (a form of processed coal used in steel making) and thereby reduce 59400 TPY in Net CO2 footprint.
There yet remain challenges for us. Despite the growing interest in Ossus green hydrogen as a replacement for existing fossil fuel sources, the gap in rapid scale-up has turned into a “chicken or egg” problem.
Some key stakeholders in the sector first want the price of green hydrogen to compete with existing fossil fuel-derived grey hydrogen – thus routing it to the ammonia, urea, fertilizer, and refinery sectors – where current consumption is highest by volume (~5.5 million tonnes per year). Others want price to be secondary and believe that the availability of larger volumes and cheaper-priced renewable energy for splitting water to hydrogen (even at a premium price) has the capacity to replace fossil fuels across multiple sectors including, but not limited to, transportation (road, sea, air going beyond long haul), power (renewable power to hydrogen and back to power) and hard-to-abate sectors such as steel, chemicals even traditional energy sector.
We see ourselves as humble purveyors of a commodity product. We want to offer our partner clients the opportunity to replace fossil fuels with Ossus Green Hydrogen today – and not debate on supply chain issues or consider it to be glamorous or futuristic by growing into the potential of a vast resource available in their own backyard.
Hi, it\’s very detailed and intriguing explanation. Plz look into the prospects of making a retail customer part of such angel investing
It\’s great to know about Ossus, very good detailed write-up that describes the company in simpler language.
Great Technology combining both Circular economy and decarbonisation. Such solutions are very much required to meet our Net Zero goal.
That what Ossus is doing a great solution to the worst humanitarian crisis our planet and future generations are facing.
Yes, I will read in more depth and revert and also try to be part of that team on a voluntary basis as I am Tier III & IV guy, back to roots after the toxix Tier i & Ii.
I too have a great proven solution for mass giga ton decarbonization, which needs scaling up.
Once I get realistically engaged, we talk and walk the talk.
Kudos Dr. Suchira Rao & her team.
Let us not find solutions but implement it together for the greater good. My heartfelt thanks to Zerodha team for their contribution and engagement
Best Wishes
Vijay Shiraguppi
MD
Techno Carbon Fiber Stone Technologies India Pvt. Ltd.
(A Indo-German Collaboration venture)
CellL +91 80730 89399.
I really liked the simple description of the vision and the explanation of the process. I helped write a report around hydrogen use and energy cluster in the port of Wilhelmshaven (in Germany).
I am really happy to know about Ossus. Thanks for sharing.